Hall-A.
Recycling flare gas from the Steel Industry.
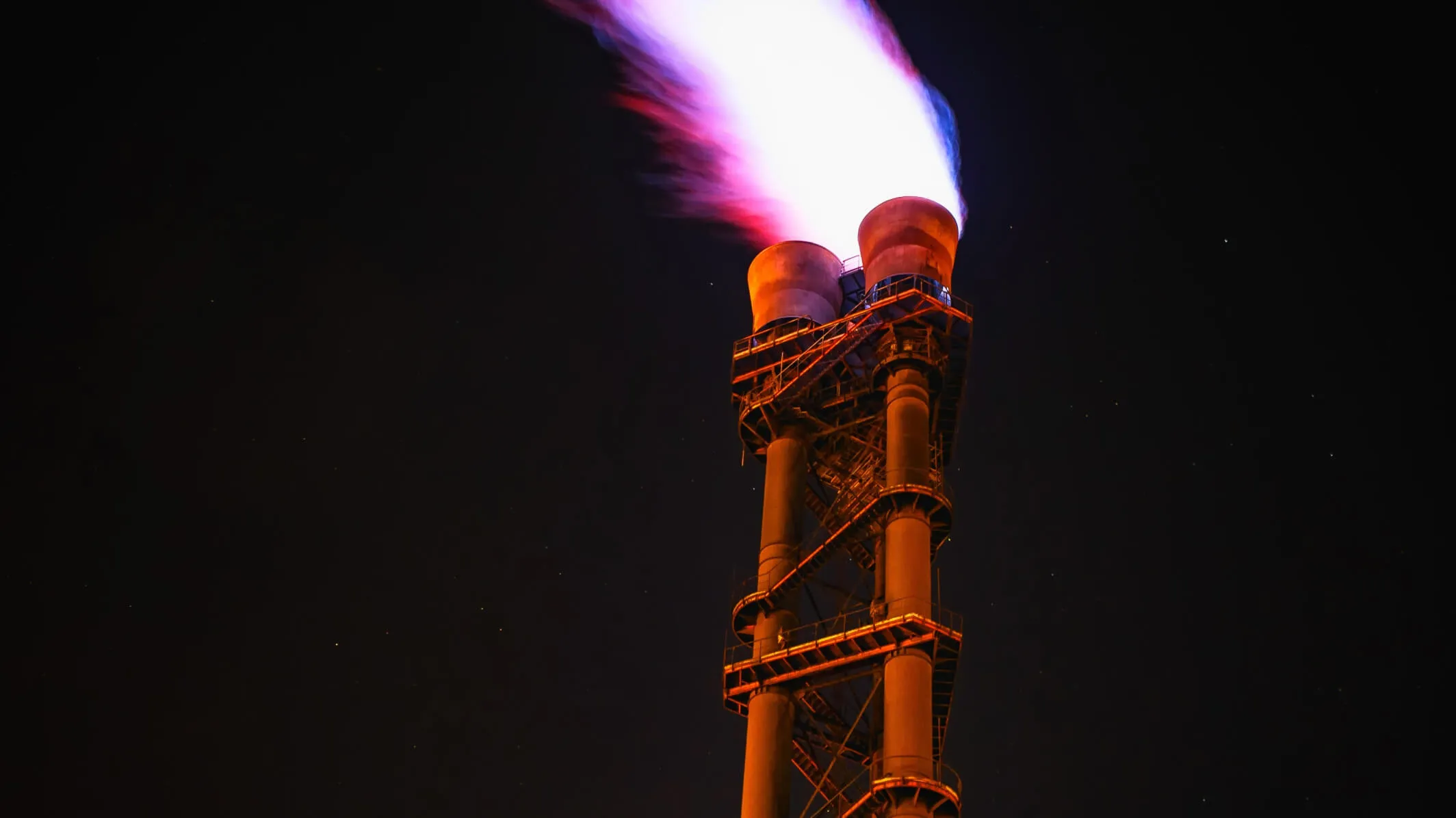
The name of the project refers to Kraftblock's production hall. Here, high-temperature heat is used to decarbonize heat. Flare gas from a local steel company is burned, stored, transported and connected to a docking station. The use of flare gas is a project funded by the EU as part of the Horizon 2021 program.
Energy data
Flare gas is a huge energy issue in the steel industry and will remain for decades in the primary steelmaking route. Often it is already used in various processes, but much of it is flared due to the mismatch between production and demand. Kraftblock aims to use flare gas directly in steel mills to support the decarbonization of the steel sector. Especially in Germany, flare gas might be a substantial part of avoiding fossil fuels. The EU data show that abput 10 TWh of energy are lost in flaring here, a great source of energy to lower the need of fossil fuel in the steel industry.
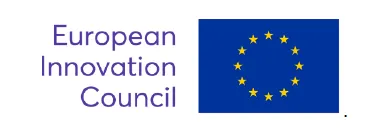
This project is funded by the European Commission within the European Innovation Councils Horizon 2021 program under project number 190167786.