Improving the Carbon Footprint of Hydrogen
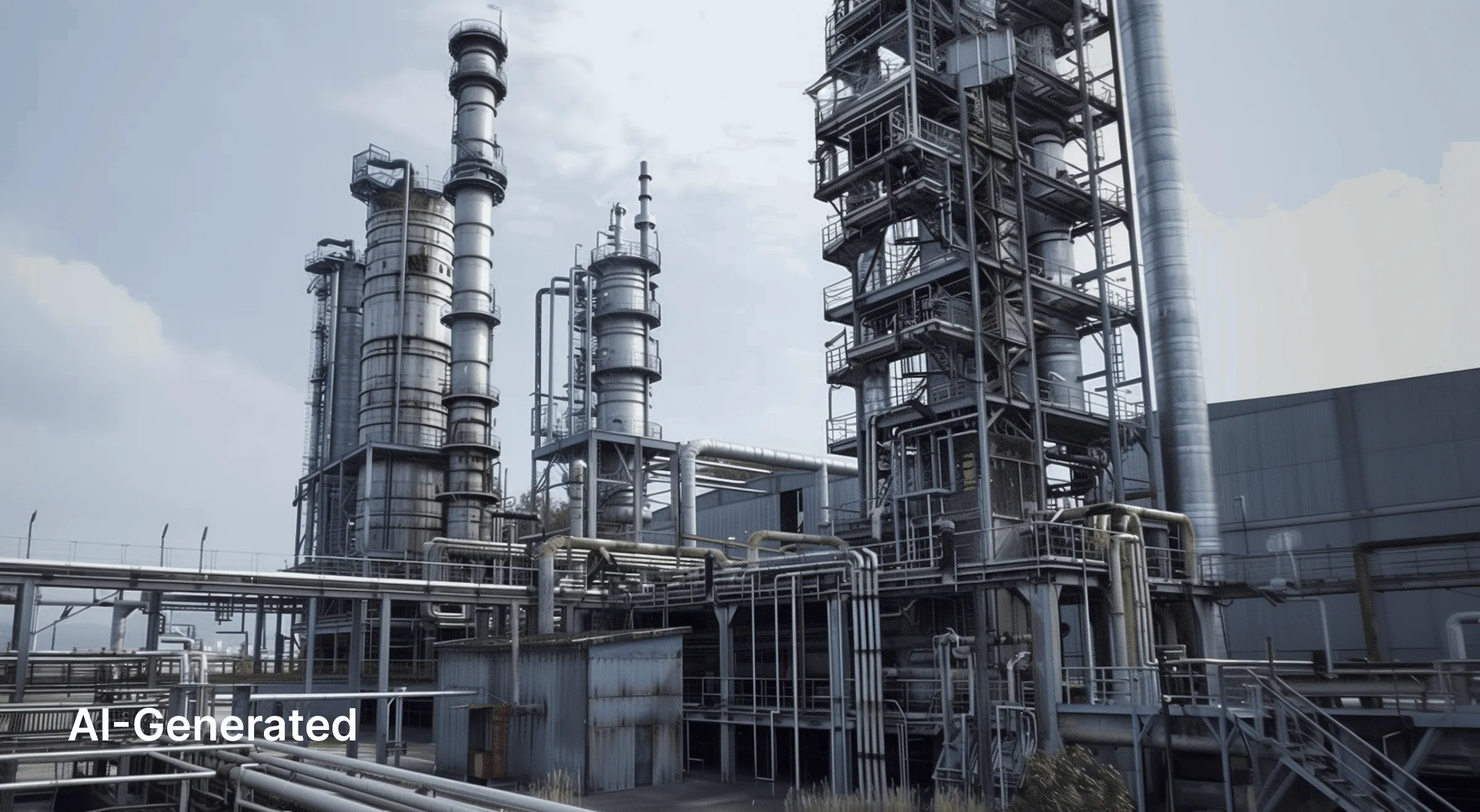
Green hydrogen is frequently regarded as a pivotal solution in the energy transition, offering a comprehensive approach to addressing various aspects of decarbonization that may not be fully addressed through electrification and battery technologies. However, the current reality is that there is no green hydrogen available, not even for processes with no other viable solutions, such as ammonia and direct reduction in steel. Today's hydrogen production continues to be an emission-intensive industry. Conventional production methods require enhancement to meet current demands. Meanwhile, the research and development efforts of electrolyzer companies can address the issue of stack lifetime to make green hydrogen become reality.
Hydrogen is the only fuel globally accepted as an environmentally benign secondary form of renewable energy. A statement that some may find confusing. Unlike fossil fuels, hydrogen is not readily available in nature; it is bound to compounds like water (H2O) and hydrocarbons like methane. As an alternative to fossil fuels, hydrogen has the highest energy content of any known fuel (122 kJ/g), 2.75 times greater than hydrocarbon fuels (Kapdan and Kargi 2006). Its byproduct is water. This means hydrogen is a clean, high-performing fuel, but current production pathways emit greenhouse gases (GHGs), see Figure 1.
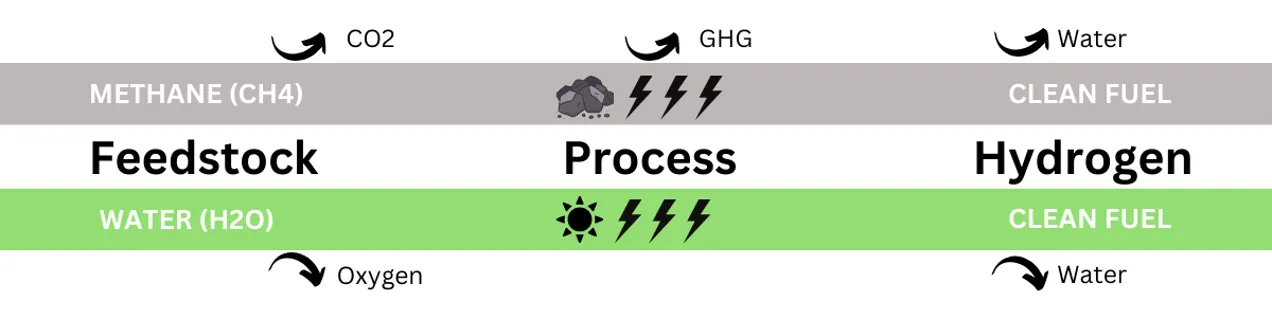
Simply put, the main caveat is obtaining hydrogen, not using it. While water is an ideal source of hydrogen, research reports indicate that 48% of hydrogen production currently derives its supply from natural gas (e.g., methane), 30% from heavy oils and/or naphtha and 18% from coal (summarized under grey hydrogen). In other words, commercially ready and dominant processes to produce hydrogen rely on hydrocarbons.
However, green hydrogen, which uses water and renewable electricity, is a hope that has not yet materialized. In the EU, only 0.4% of hydrogen is from green electricity (KfW 2024). Projects stops and bankrupcies of hydrogen companies leave many in doubt. This raises the question: What can be done to reduce emissions from today’s hydrogen production?
Can Hydrogen Demand be Met with Green Production
Future demands for hydrogen production, generally, are driven by the race to reduce reliance on fossil fuels, stabilize geopolitical tensions, and strengthen energy independence. And what once made low emissions or green hydrogen expensive, energy waste and efficiency, could now drive its affordability through heat upcycling, renewable energy integrations, and green energy storage systems.
In 2023, demand for low-emission hydrogen increased by 10% but remains below 1 Mt. Recent estimates indicate that about 95% of the hydrogen obtained today (74 million tonnes) generates 830 million tonnes of CO₂ yearly (MIT Climate Portal). According to the 2020 production estimate, current demands of hydrogen are primarily supplied via black coal (19%) and the majority (59%) through natural gas.
While that ratio is somewhat lackluster, these hydrogen production pathways contribute about 2% of the total estimated global CO₂ yearly. Should demand increase, as is projected, then yearly contributions of CO₂ would follow accordingly.
Governments are building efforts to foster market growth by introducing mandates, incentive programs, and strategies (IEA, 2024). Especially in the EU, billions are invested in projects. These committed initiatives signal a future demand for low-emission hydrogen with projections of up to 1.5 Mt per year by 2030, tripling current demand (IEA, 2024). According to McKinsey & Company (2023) projections, clean hydrogen demand could surge 100 times, reaching between 125 and 585 Mt per year by 2050.
Future demand is expected to be initially driven by existing applications transitioning to clean hydrogen, with emerging applications such as steel production and feedstock for the chemical industry contributing more substantially post-2030. While the demand is there, it lacks realization of clean, affordable hydrogen.
Transitioning to Low-Emission Hydrogen Production
Affordable green or blue hydrogen may not be realistic in the next decade. While green hydrogen would be three times as expensive today, by 2030 it would optimistically be twice as expensive. The cost of electricity is a prerequisite, but it is also the electrolyzer technology that is not suitable for competitive hydrogen prices: Because the electrolyzer stacks are not designed for flexible use and thus low electricity prices, and because they need to be replaced every two years, the hardware costs are unsustainable. This issue needs to be addressed in research and development. However, there is a silver lining to the problem of low efficiency: high-temperature electrolysis holds out the promise of a much more efficient process that could reduce the cost by reducing energy losses
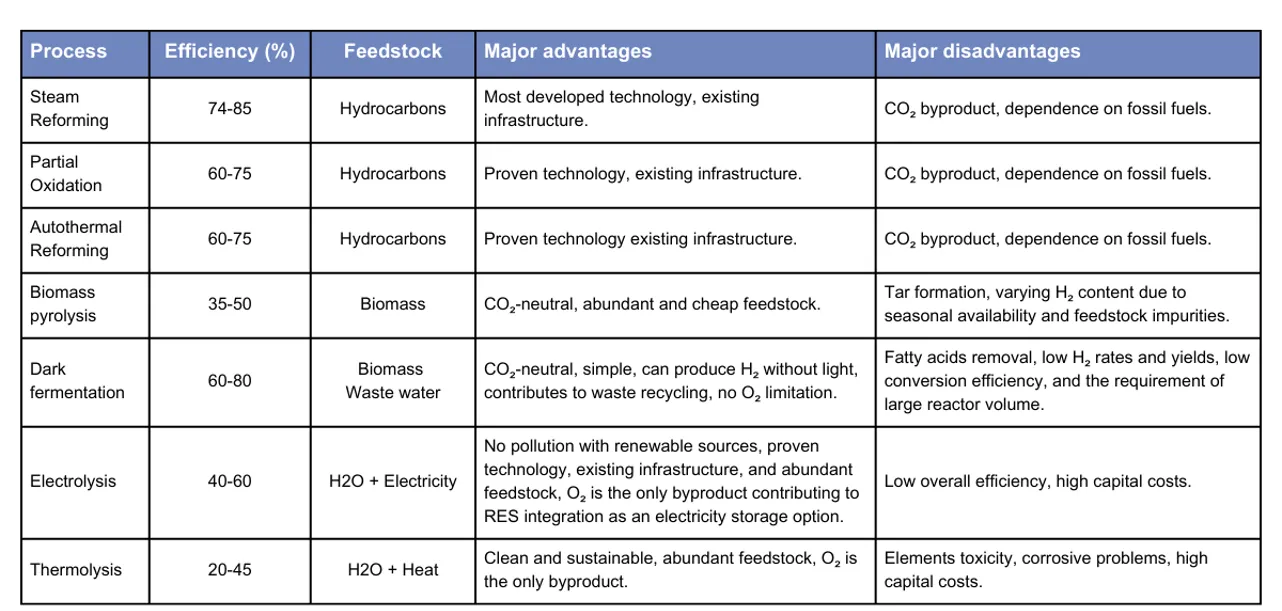
The fueled current demand could result in an increased hydrogen production from fossil fuels. This conventional production pathway is outlined in Figure 2 and maintains dominance due to commercially available infrastructure and know-how. With this, the need for lowering the emissions of black or gray hydrogen becomes an important goal.
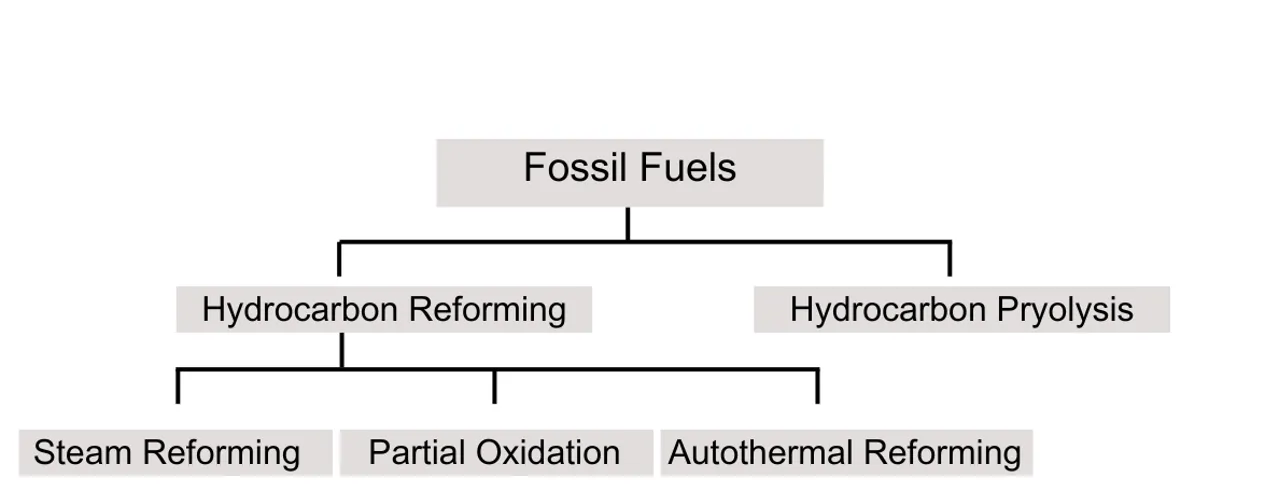
Substantial Heat and Energy Needs for Steam Methane Reforming (SMR)
The most widely deployed and cheapest method for hydrogen production today is steam methane reforming (SMR), which accounts for about half of the world's hydrogen production. The estimated marginal production cost of hydrogen by SMR was 3.5 EUR/kg. Carbon capture installations increased this price to 4.41 EUR/kg (European Hydrogen Observatory, 2023). Reliance on grid electricity doubled these 2023 estimates.
Despite the feedstock, generating high temperatures can be costly. Still, high temperature is required for most known processes to achieve the necessary reaction kinetics and ensure efficient conversion into hydrogen (see Figure 3).
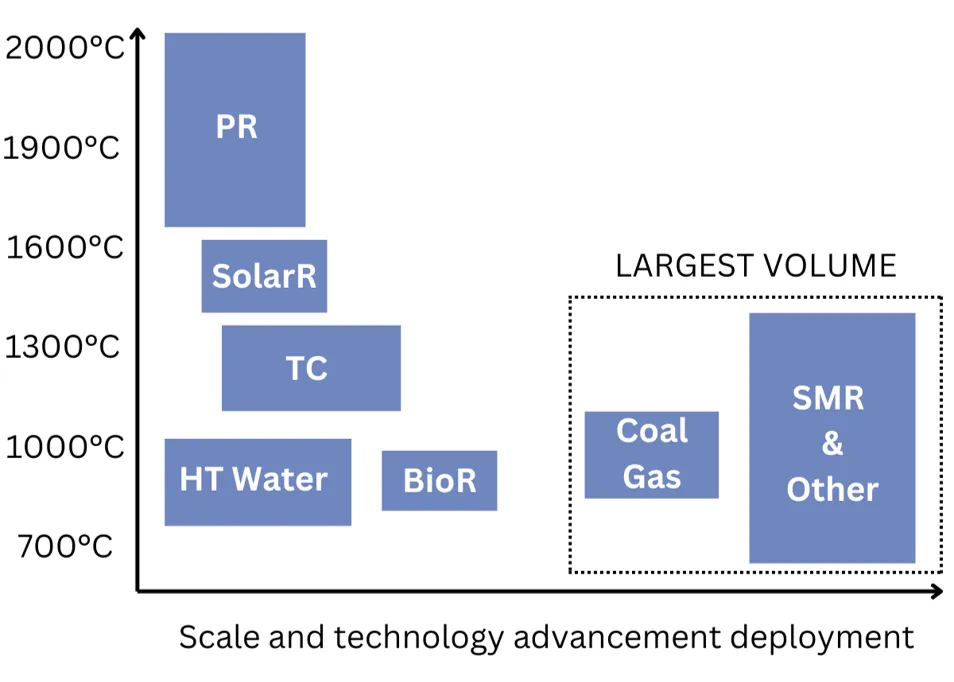
Figure 3: Temperature requirements to drive various hydrogen production relative to scale and technology deployment showcasing substantial needs for heat and or energy across processes and pathways such as plasma reforming (PR), solar reforming (SolarR), thermochemical cycles (TC), Biomass gasification (BioR), coal gasification (Coal Gas) and steam methane and other hydrocarbon reforming (SMR). Adopted and modified from Muritala et al., 2020.
How to Improve the carbon footprint of SMR
There is a mix of electrification and waste heat recovery that can lower the emissions of the process. The steam needed can be provided by electricity. Kraftblock’s storage system charges electricity when it's cheap and avoids high prices. Thus, electricity gets competitive or even cheaper than natural gas, the usual fuel for steam generation. Upcycling waste heat generated throughout SMR can significantly improve the process. The water-gas shift reaction and flue gases from the reformer release substantial excess heat. This thermal energy is lost without proper recovery systems, resulting in reduced overall efficiency and increased energy demand.
How it works:
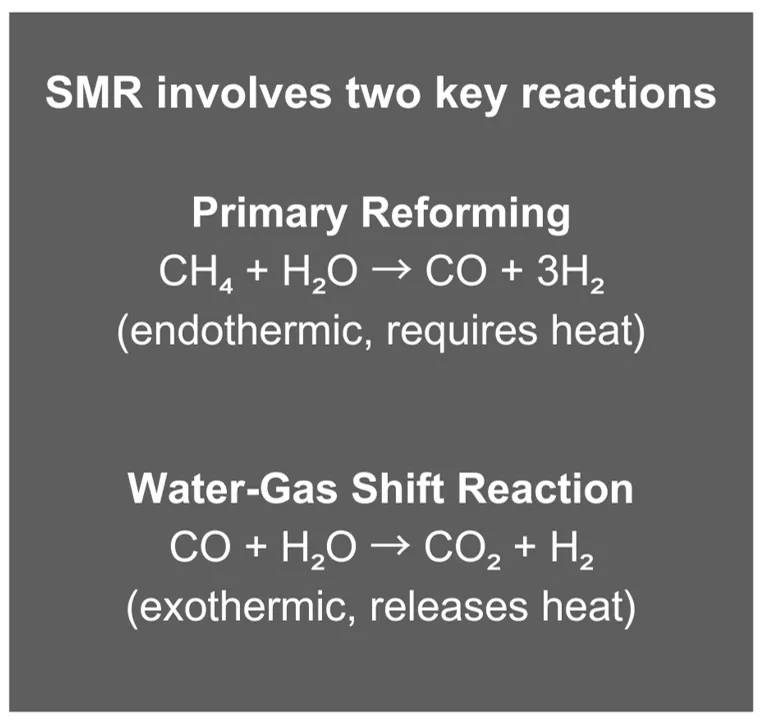
The primary reaction of SMR operates at temperatures between 700°C and 1,000°C and pressures ranging from 3 to 25 bar. In this process, a mixture of steam and methane passes over a nickel-based catalyst, facilitating the endothermic reaction that produces hydrogen.
Gasification processes operate at even higher temperatures, typically above 800°C. They are often integrated with steam reforming, converting carbonaceous materials into syngas (a mixture of hydrogen and carbon monoxide) before undergoing further steam reforming to enhance hydrogen yield.
Optimizing Flue Gas Heat Recovery
The combustion process in an SMR unit generates flue gas, which exits the reformer at approximately 1,000°C before being cooled to temperatures below 180°C in the convection section. This provides a significant opportunity for waste heat recovery and reuse, particularly in:
- Preheating Boiler Feedwater: The hot exhaust gases (800–1,200°C) can be redirected to preheat water entering the boiler or a heat recovery steam generator (HRSG), thereby reducing the external energy required for steam generation. Using a high-temperature storage, the energy can be made flexible for operations.
- Supplementing Process Steam: Recovered heat can also be utilized to generate steam with storage and waste heat steam generator, thereby reducing fuel consumption. The steam generation can be combined with electricity: High-temperature electrification with storage allows for low energy costs.
- Natural Gas Preheating: The hot effluent gas from SMR can preheat the incoming methane feedstock, lowering the energy input required for reforming.
- Combustion Air Preheating: Integrating a preheating air system enhances burner efficiency, reducing overall fuel consumption while maintaining the high temperatures required for SMR.
Boosting efficiency of green hydrogen production
It also will be relevant to improve energy efficiency and costs in green hydrogen production. Ideas for that involve Kraftblock storing green heat from excess renewable electricity, deploying it as heat for solid oxide electrolyzers (SOEC). SOEC utilizes elevated temperatures ranging from 500°C to 1000°C to enhance the efficacy of electrolyses. The Kraftblock Net-Zero Heat System is capable of producing steam at a low cost, which can be utilized in the process. Additionally, the system can replace the heating elements of the electrolyzer, thereby ensuring a stable heat supply from flexible times and reducing costs associated with this portion of electricity usage.
There are also a lot of other methods to produce hydrogen and ways to increase performance that cannot be depicted altogether in this article.
Conclusions for cleaner hydrogen production right now
Unfortunately, due to the slow market readiness for green hydrogen, a phased approach is necessary to lower the carbon footprint of hydrogen. The retrofitting of existing hydrocarbon-based systems to function on green electricity and waste heat recovery, if not already implemented, can serve as a transitional measure. The integration of thermal storage systems, which facilitate the provision of affordable heat, has been demonstrated to contribute to the economic viability of green hydrogen production. The application of high-temperature electrolysis holds considerable promise in surpassing alternative methods due to this enhancement.
References
Diéguez, P., Ursúa, A., Sanchis, P., Sopena, C., Guelbenzu, E., & Gandía, L. (2008). Thermal performance of a commercial alkaline water electrolyzer: Experimental study and mathematical modeling. International Journal of Hydrogen Energy, 33(24), 7338-7354. https://doi.org/10.1016/j.ijhydene.2008.09.051
Dincer, I., & Acar, C. (2017). Review and evaluation of hydrogen production methods for better sustainability. Renewable and Sustainable Energy Reviews, 67, 597–611. https://doi.org/10.1016/j.rser.2016.09.107
European Hydrogen Observatory. (n.d.). Cost of hydrogen production. Retrieved from https://observatory.clean-hydrogen.europa.eu/hydrogen-landscape/production-trade-and-cost/cost-hydrogen-production. Date of last access Feb 11, 2025
IEA, D. (2021). Global Hydrogen Review 2021. Public Report
IEA (2024), Global Hydrogen Review 2024, IEA, Paris https://www.iea.org/reports/global-hydrogen-review-2024, Licence: CC BY 4.0
IRENA (2020), Green Hydrogen Cost Reduction: Scaling up Electrolysers to Meet the 1.5⁰C Climate Goal, International Renewable Energy Agency, Abu Dhabi.
Ivy, J. (2004). Summary of electrolytic hydrogen production: Milestone completion report (NREL/MP-560-36734). National Renewable Energy Laboratory. https://www.nrel.gov/docs/fy04osti/36734.pdf
Kalamaras, C. M., & Efstathiou, A. M. (2012). Hydrogen Production Technologies: Current State and Future Developments. Conference Papers in Science, 2013(1), 690627. https://doi.org/10.1155/2013/690627
Kapdan IK, Kargi F. Bio-hydrogen production from waste materials. Enzym Micro Tech 2006; 38:569e82.
Muritala, I. K., Guban, D., Roeb, M., & Sattler, C. (2020). High temperature production of hydrogen: Assessment of non-renewable resources technologies and emerging trends. International Journal of Hydrogen Energy, 45(49), 26022-26035. https://doi.org/10.1016/j.ijhydene.2019.08.154
McKinsey & Company. (2023). Global energy perspective 2023: Hydrogen outlook. Retrieved February 5, 2025, from https://www.mckinsey.com/industries/oil-and-gas/our-insights/global-energy-perspective-2023-hydrogen-outlook
MIT Climate Portal. (n.d.). Hydrogen. Retrieved from https://climate.mit.edu/explainers/hydrogen
Wappler, M., Unguder, D., Lu, X., Ohlmeyer, H., Teschke, H., & Lueke, W. (2022). Building the green hydrogen market – Current state and outlook on green hydrogen demand and electrolyzer manufacturing. International Journal of Hydrogen Energy, 47(79), 33551-33570. https://doi.org/10.1016/j.ijhydene.2022.07.253